Procurando manter-se na vanguarda da indústria, a Bugatti acaba de anunciar a sua mais recente inovação: pinças de travão monobloco de oito pistões que, uma vez produzidas, serão as maiores já vistas na indústria automóvel. Com uma particularidade adicional: são fabricadas não segundo os métodos tradicionais, mas por impressão 3D.
De acordo com a marca de superdesportivos de luxo de Molsheim, estas novas pinças são produzidas em titânio, solução que permite reduzir o peso deste componente para 2,9 kg, contra os actuais 4,6 kg que pesa, cada uma, hoje em dia.
Em termos de volume, este é o maior dos componentes funcionais já produzido em titânio, através de métodos de fabricação aditivos”, sublinha o chefe de Novas Tecnologias da Bugatti, Frank Götzke. “Qualquer pessoa que olhe para este novo componente ficará surpreendida com o quão leve é, apesar do seu tamanho. Tecnicamente, é também uma pinça de travão extremamente impressionante, além de ter um aspecto lindo.”
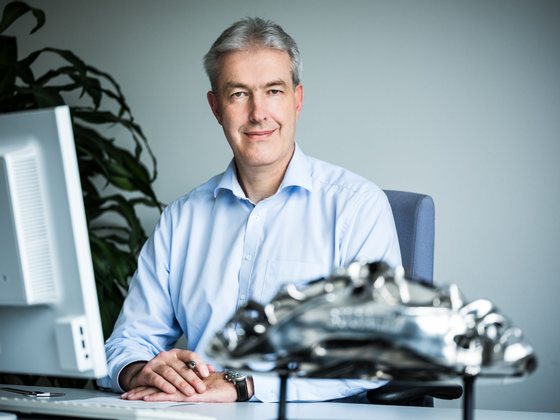
Frank Götzke
Segundo a Bugatti, cada uma destas pinças leva cerca de 45 horas a produzir. Com o processo a iniciar-se com o derretimento de pó de titânio, de modo a produzir uma substância aquosa, recorrendo para tal a quatro lasers de 400 watts. Após uma impressão que implica a sobreposição de 2.213 camadas, a peça passa por um tratamento a quente, para torná-la mais resistente, seguindo-se uma etapa de nivelamento e suavização. Finalmente, uma espécie de moinho de cinco eixos maquina todos os contornos funcionais da peça, à imagem do que acontece nos pistões.
Terminado o longo processo, a pinça obtida é muito mais resistente do que aquelas que o Chiron actualmente utiliza, nota o próprio fabricante, explicando que para tal contribui o facto de recorrer a uma liga específica de titânio, já utilizada, por exemplo, na carenagem inferior e nas asas dos aviões.
A Bugatti revela ainda que pretende dar início à fase de testes, em ambiente real, com estas novas pinças de travão, ainda na primeira metade deste ano. Garantindo, simultaneamente, que continuará a trabalhar no sentido de diminuir os tempos de produção.
A marca francesa está, actualmente, a avaliar a produção de outros componentes, com recurso à impressão 3D. Por exemplo, um limpa para-brisas em alumínio com 63 cm de comprimento, igualmente impresso em 3D, que pesa apenas 400g, ou seja metade do peso do componente actual produzido em alumínio forjado, sem perder rigidez.